Introduction to Computational Fluid Dynamics (CFD)
In contemporary engineering, Computational Fluid Dynamics (CFD) simulation is an important technology. As one of the Computer-Aided Engineering (CAE) techniques, it helps engineers in solving difficult issues and allows for the full analysis and prediction of fluid flow or heat transfer characteristics. Using high-performance computers, these simulations aid in the comprehension of intricate relationships in liquid or gas systems.
This article introduces the fundamentals of the technology behind Computational Fluid Dynamics processes along with their significance and real-world examples of their applications. If you’re looking to implement CFD innovation, rest assured that our experts at ASHO Engineering will help you reduce costs and optimize your processes.
→ Get It Now: Free Consultation For Your Project ←
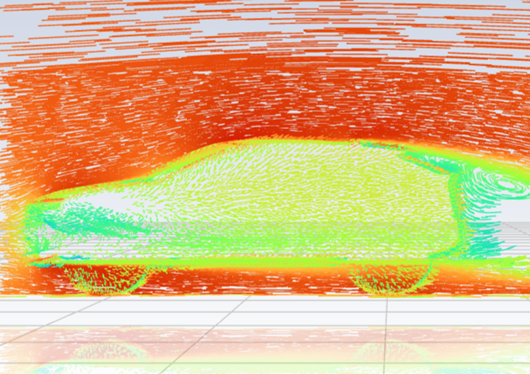
Fluid Flow Vs Fluid Dynamics
1. Fluid Flow
Whether it’s kerosene in an airplane engine, gas in industrial turbines, air in the atmosphere, or even blood in blood vessels, the movement of a liquid or gas from one place to another is called fluid flow.
More technically, fluid flow is the movement of particles contained in a liquid or gas from one point in space to another.
This movement of matter can be characterized by elements such as flow rate, pathway, or velocity.
The flow rate represents the amount of fluid moved in a given period of time. Velocity, on the other hand, is the speed at which particles move at a given point in the flow. The term “given point” is important to emphasize because this velocity is not always uniform and varies depending on the type of flow.
The type of fluid flow is defined by two factors. The first one is the configuration of the system itself (where the fluid is located) and the other is the external forces applied to the fluid. We can then distinguish two major types of flow:
- The laminar flow, generally observed in a high-viscosity fluid, is characterized by its smoothness, parallel particle motion with little or no mixing
- The turbulent flow, generally observed in low-viscosity fluids, is characterized by chaotic and irregular motion with mixing of the different layers.
2. Fluid Dynamics
Fluid dynamics, on the other hand, encompasses not only the fluid flow concepts mentioned above, but also several mathematical and mechanical parameters, such as forces and pressure analysis.
This combination of numerous variable parameters makes predicting the motion of a fluid a difficult task. Fortunately, Computational Fluid Dynamics has made the processing of these complex equations more accessible. This simulation technique performs complex calculations that consider all of these variable parameters in order to predict fluid behavior under specific conditions as reliably as possible.
Boundary conditions, such as channel shape and surface roughness, and external forces, such as gravity and pressure gradients, also play a critical role. The fluid’s specific properties, such as viscosity and density, directly affect the transition between laminar and turbulent flow, adding to the complexity of fluid dynamics.
Among the many parameters to be considered, are physical principles such as:
- Conservation of mass, with the continuity equation
- Conservation of momentum, through the Navier-Stokes equations
- Conservation of energy, with Bernoulli equation.
And on the other hand, boundary conditions such as:
- Dynamic boundary conditions, related to the viscosity of the moving fluid
- Kinematic boundary conditions, related to the physical properties of the wall along which the fluid flows.
What is Computational Fluid Dynamics (CFD) ?
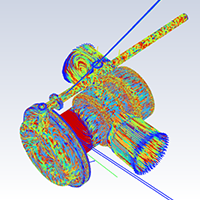
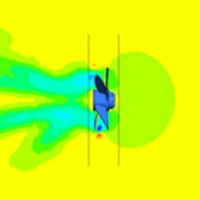
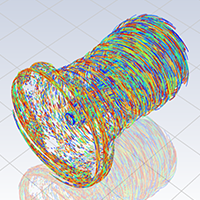
As its name suggests, CFD is a set of computer processes designed to numerically mimic the behavior of fluids and gas (such as water or air) and their interactions with the elements inside their environment. It is performed by engineers using specialized Computational Fluid Dynamics software such as SolidWorks, Ansys, SimScale, and AutoDesk, to name but a few.
Using these CFD tools, engineers can create virtual 3D models, to simulate real-life situations. This might involve analyzing airflow around a high-speed car, the movement of water inside a duct, or the transfer of heat inside any industrial equipment. These CFD analyses provide engineers with reliable information for optimizing a product, even before designing a prototype.Driven by innovation and passion, we at ASHO Engineering offer you the full value of CFD techniques, meticulously tailored to your precise needs. To help you achieve your goals, Let’s get in touch.
Why use Computational Fluid Dynamics (CFD) ?
The origins of CFD simulation techniques date back to the 1950s. Since then, and with the advent of increasingly powerful computers, simulation techniques have continued to evolve. So much so that today this technology occupies a prominent place in a wide range of industries. There are several reasons for this Computational Fluid Dynamics growing adoption, and they can be summarized as follows:
- Refine Product Design and Save Time
- Reduce Product Development Costs
- Increased Capacity for Innovation
- Better Management of Equipment-related Risks
1. Refine Product Design and Save Time
Product development is a complex process. It takes place in several stages, from ideation to market launch, and includes the essential step of prototyping.
Prototyping enables engineers to carry out tests under real-life conditions and to gather information on product performance, ergonomics, and overall design. A product may require several prototyping phases before it can be brought to market.
Using Computational Fluid Dynamics tools, a large proportion of real-life testing can be carried out virtually, thanks to simulation processes. This saves time in product development and enables companies to fine-tune the prototype before it is even manufactured.
For example, Computational-Aided Dynamics can be used to adjust elements as insignificant as the shape of bumpers or rear-view mirrors, to study the drag in each case and thus improve a car’s energy efficiency, all virtually.
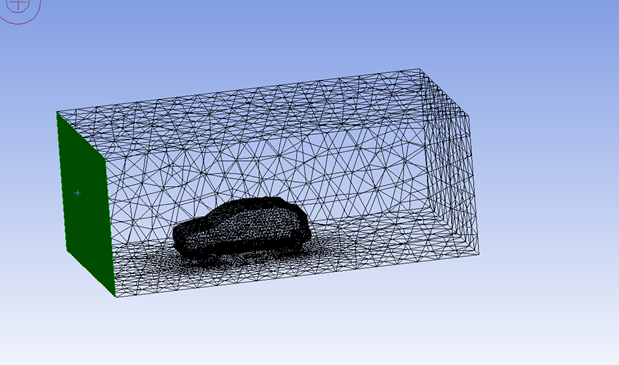
2. Reduce Product Development Costs
Typically, in engineering a product development process can involve the production of several prototypes. The aim is to obtain an optimum final prototype which will serve as a model for the manufacture of the product to be marketed.
Thanks to CFD, several test phases can be carried out virtually. This reduces the number of prototypes to be manufactured before the final one, ensuring a reduction in product development costs.
3. Increased Capacity for Innovation
It is a well-known fact: innovation is expensive. A new product requires significant expenditure, not least because the testing phases are generally longer when you’re exploring uncharted territory. What’s more, products must comply with current norms and standards. Computational Fluid Dynamics simulation increases the scope for innovation, as it facilitates the exploration of new concepts without being limited by the constraints of a traditional development process.
For example, it enables engineers to create prototype models virtually and test them in simulation under conditions that are very close to real-life conditions..
4. Better Management of Equipment-related Risks
By identifying potential problems early in the design process, CFD simulation enables engineers to avoid errors with potentially costly consequences. Computational Fluid Dynamics tools enable complex scenarios to be analyzed much more easily than traditional processes.
For example, it can be used to study the behavior of equipment subjected to extreme conditions, which are difficult to test physically. These could include the effect of severe weather conditions, high speeds, pressures, or extreme temperatures on an artificial system or a particular component.
04 Practical Examples of The Use of Computational Fluid Dynamics
1. Computational Fluid Dynamics In the Aeronautics Sector
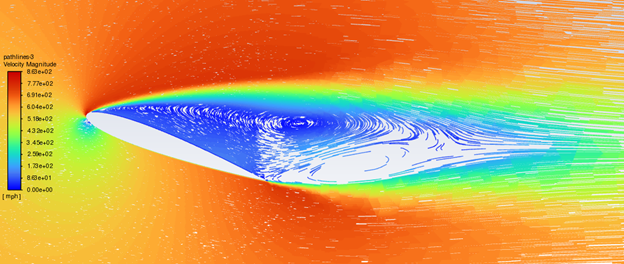
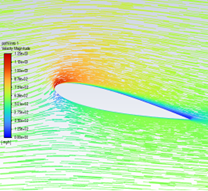
Computational Fluid Dynamics simulation is particularly useful in the field of aeronautics. It helps to improve the design and safety of flying machines such as airliners. It’s used by engineers to study aircraft aerodynamics. Sure, it would be difficult to analyze in real life the performance of a plane full of real passengers and subjected to extreme conditions. Computer-Aided Simulation makes it possible to study the most extreme situations, with the aim of producing ever more efficient and reliable equipment.
When it comes to aircraft, many key components can be improved through simulation. These include elements such as specific wing geometries, propellers and turbines, as well as engine de-icing and cooling systems.
By testing the structure of aircraft wings, engineers study its aerodynamics, focusing on energetic efficiency (more safety and less fuel). By working on factors such as angle of attack, it is possible to maximize lift and minimize drag.
However, fuel efficiency is not only determined by the geometry of aircraft wings. Turbine and propeller performance is also critical. Simulations are carried out by modeling the airflow in contact with the components. The intensity of the forces acting on the blades, the pressure experienced and the turbulence generated, provide engineers with invaluable information for optimizing the global aerodynamics of flying machines.
Aircraft fuel efficiency is a priority, but passenger safety is even more so. Overheating or malfunctioning of de-icing systems can jeopardize the safety of the aircraft and, by extension, its passengers. In such a context, any method that can safely test aircraft operation under extreme conditions is a major asset. These computerized techniques have opened the door to all these possibilities, limited only by the expertise of the engineers who use it.
→ Free Quote – Discuss with a CFD Engineer ←
2. Computational Fluid Dynamics for Better Management of Equipment-related Risks
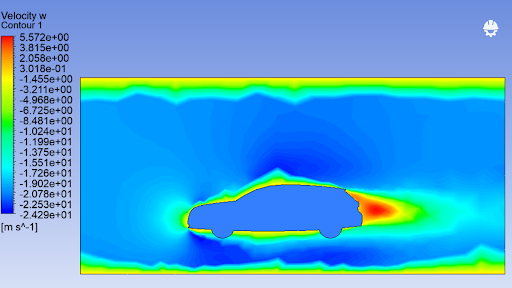
As in the previous sector, simulation processes are becoming increasingly integrated, enabling approaches that were previously unattainable. In modern industry, Computational Fluid Dynamics has developed rapidly, and thanks to this technological advance, the design of certain types of vehicles is now possible for engineers.
Clearly, It is now possible for engineers to:
- Reduce manufacturing costs by optimizing designs before production
- Analyze the impact of external conditions on individual vehicle parts
- Improve vehicle components to minimize drag and lift
- Optimize engine heat regulation
- Avoid any risk of fire or malfunction by studying the movements of the various fluids inside the vehicle’s ducts as they heat up when the engine is started. Etc.
3. Computational Fluid Dynamics In Climatology and Meteorology
If you’ve ever wondered how meteorologists and climatologists predict weather and climate conditions, you should know that they also use CFD simulations. The principle remains that this method enables complex calculations to be carried out based on available data.
More specifically, this application enables scientists to:
- Analyze atmospheric conditions in different regions to better understand and predict their variations
- Optimize forecasting models and refine their accuracy
- Analyze complex natural phenomena, in particular hurricane formation, to determine their trajectory and intensity. Thanks to this anticipation, the risk of natural disasters is considerably reduced
- Analyze air quality, forecasting the dispersion of pollutants in the atmosphere and their short- and medium-term impact.
4. Computational Fluid Dynamics In Healthcare and Biomedical Sector
With the development of ever more powerful computers and software, the applications of fluid dynamics in the biomedical sector abound. Through technical simulations, 3D models of all or part of the human body have enabled us to gain a deeper understanding of fluid movement within the human body.
Whether to analyze the movement of liquids or air inside the body’s organs, track the bio-kinetics of drugs and other substances, develop medical devices, or plan surgical interventions, CFD simulations have opened the way to possibilities that were unimaginable just a few years ago.
Here are some examples of Computational Fluid Dynamics applications in this sector:
- Drug delivery systems that help in optimizing drug dispersion and absorption
- Blood flow analysis: to be able to design stents and other artificial heart valves
- Development of adapted medical devices: ventilators and dialysis machines
- Biomechanics: helps improve prosthetics and implants
- Tissue engineering: to ensure nutrient transport in bioreactors
- Non-invasive diagnostics: Virtual simulations for patient conditions
- Infection control: Model pathogen spread in facilities
- Public health: Simulate contaminant spread for outbreak response.
The importance of CFD simulation is well known. Its versatility makes it easily adaptable to all areas of research and development. Based on the analysis of fluid dynamics, it helps to optimize designs and their performance, reduce costs, facilitate innovation, and ensure better management of equipment-related risks.
Many industries are experiencing unprecedented growth by implementing computerized techniques into their processes. These include aerospace, automotive, climatology & meteorology, and biomedical, to name a few.
The advances in this simulation are also significant because its technology is still in its infancy. The field of possibilities is therefore immense.
Whatever the industry sector, the rise of Computational Fluid Dynamics technology has offered numerous possibilities. When professionally handled, the best results are guaranteed. For more information on how Computer-Aided Engineering (CAE) can benefit your projects, feel free to read the Introduction to CAE article.
Our experts are ready to assist you in embracing innovation. Contact Us now, and benefit from the best in Computational Fluid Dynamics technology.
We look forward to working with you!
Share this post, don’t forget!